-
2103 Room NO.322 Xinggang One Road,Haicang District,Xiamen Fujian,China

Are Oversized PV Modules a Major Cause of Solar Plant Collapse?
Table of Contents
Industry Status: Frequent Accidents and Reflections
Driven by global carbon neutrality goals, the construction of solar power plants has rapidly expanded, especially in regions like China’s northwest deserts and offshore sites. However, structural collapses of solar mounting systems have become alarmingly frequent. In some areas, multiple incidents per year are now seen as “normal” industry occurrences.
A single collapse can result in direct economic losses exceeding tens of millions of RMB. Insurance data shows that the annual industry loss has already reached several billion yuan.
While many attribute these incidents to “natural disasters” like strong winds, it raises a critical question: Why are bridges and buildings collapsing considered serious engineering defects, yet solar structure failures are often excused by blaming the weather? Given today’s mastery of wind field analysis and structural design, pushing responsibility onto uncontrollable factors is a clear evasion of underlying technical issues.
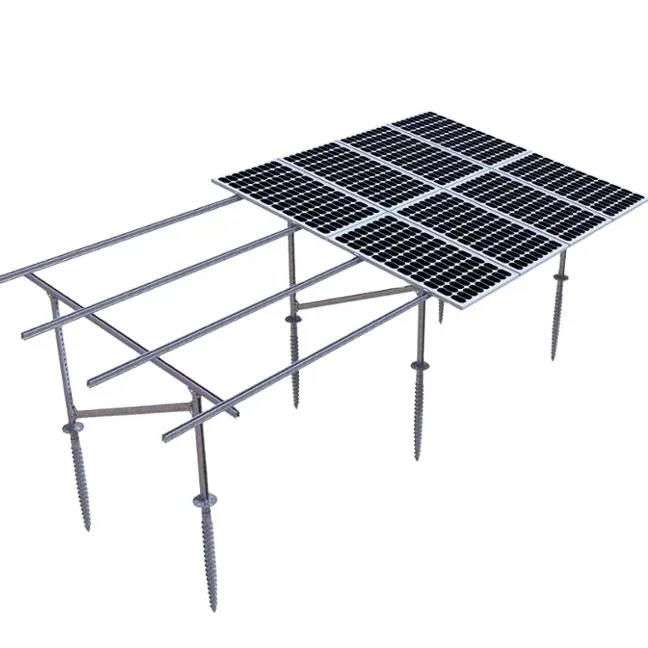
👉 Explore Reliable Ground Mount Systems
Core Problem: Structural Issues of Double-Vertical Layouts in the Era of Large Modules
1. Wind Resistance Decline Due to Larger Surface Area
- Past Adaptation: Around 2010, standard PV modules measured about 990×1650mm (1.63㎡), and double-vertical layouts had a width of about 3.3 meters, with stable wind resistance.
- Current Challenge: Today’s mainstream modules reach sizes like 1133×2287mm or even 1303×2384mm (over 3.1㎡ each). Double-vertical mounting now creates a massive wind-facing area of around 6.22㎡ — almost double the early designs.
When mounting arrays exceed 10 meters in width, their wind response begins to mimic that of small aircraft wings, requiring exponentially stronger structural support.
2. Load Amplification Under Typhoon Conditions
Large double-vertical panel areas experience significant “load amplification” effects during high winds. Field tests reveal that under 27m/s wind speeds, actual wind loads on such configurations can reach 3–5 times theoretical values — far exceeding the designed safety margins, particularly in high-wind environments like deserts and offshore farms.
3. Structural Design Dilemmas from Upper and Lower Row Disparities
Because the upper and lower panel rows face different wind exposures, aerodynamic coefficients vary by 20%-30%. To design properly, stronger north-side structures are needed, increasing material costs by up to 20%. If simplified to save costs, it leaves hidden safety risks — a systemic defect rooted in outdated layout designs.
Solutions: The Technical and Economic Advantages of Single-Vertical Row Layouts
1. Enhanced Performance
- Single-row setups reduce system height by 30%-40%, significantly lowering the center of gravity and improving anti-overturning stability.
- Each module maintains a limited wind-facing area (~3.11㎡), preventing hazardous load amplification and increasing structural safety redundancy by over 40%.
2. Cost Optimization
- Through structural innovations (modular designs, accessory improvements), single-row mounts require 10%-20% less steel compared to double rows.
- For example, at identical wind conditions, a single-row support system saves approximately 6 tons of steel per megawatt, equivalent to saving 3 million RMB for a 100 MW solar farm.

👉 Check Our Aluminum Ground Mount Options
3. Easier Construction
Single-row layouts eliminate upper-lower design discrepancies, simplifying inventory management and installation. Field tests show installation speed improvements of over 18%, which is crucial for large-scale rapid deployments — like those seen in Japan’s aggressive solar expansions across Hokkaido and Tohoku.
Industry Call to Action: Move Beyond “Certification Worship” Toward Structural Innovation
Currently, there is an unhealthy tendency to emphasize “certifications” while ignoring genuine structural design innovations. Some companies prioritize “certification stacking” to sidestep deeper technical flaws.
The essence of solar racking system safety lies in scientific structural engineering. As module sizes continue to grow, only through layout optimization, material upgrades, and digital simulation technologies (e.g., wind tunnel testing and finite element analysis) can the dual goals of safety and cost-efficiency be achieved.
We recommend:
- Design firms must update their wind load models at the feasibility study stage.
- Manufacturers should invest in R&D for single-row mounting solutions.
In the journey toward global carbon neutrality, solar plants should not become fragile projects dependent on favorable weather, but rather resilient, century-lasting infrastructures.
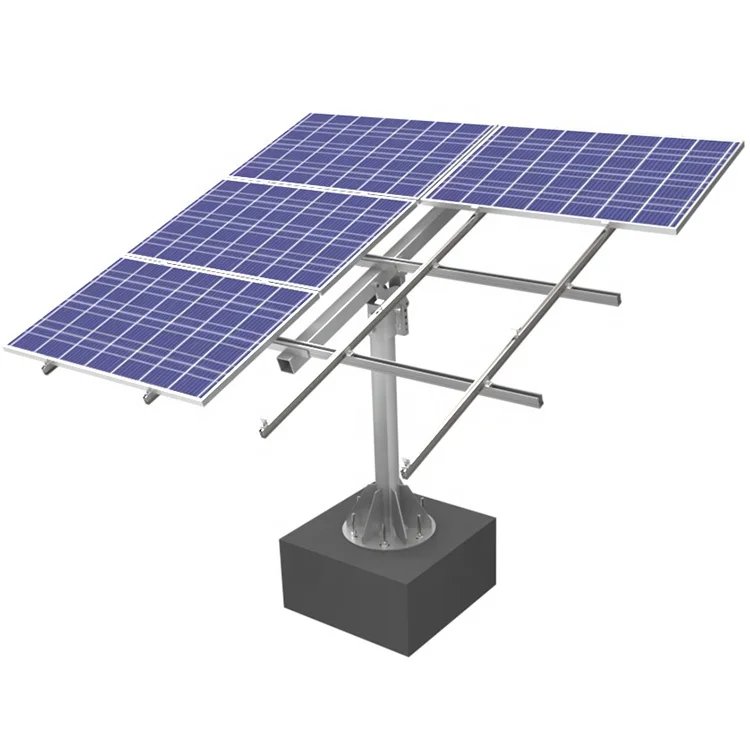
👉 Explore Our Single Pole Ground Mount Systems
Related Links for Further Reading
- 🌞 Solar Mounting System Structural Calculation Manual – International Version (Illustrated)
- 🛠️ Ground Solar Mounting System Overview
- 🌱 Agricultural Farmland Solar Mounting Systems
- 🏗️ Concrete Block Foundation for Solar Projects
- 🌊 Floating Solar Mounting System for Water Surfaces