-
2103 Room NO.322 Xinggang One Road,Haicang District,Xiamen Fujian,China
Solar Ground Screw Manufacturer
Product Discription
Hot Dip Galvanizing Ground Screw Merits:
Fast, Strong, & Eco-Friendly: Our hot-dip galvanized ground screws offer rapid installation, superior strength, lightweight design, and low-cost solutions. They minimize site disruption and are environmentally conscious.
Machine-Driven Installation: Ground screws are quickly and efficiently installed using specialized machinery, driving them directly into the ground.
Reduced Excavation & Soil Impact: Compared to concrete foundations, our ground screws significantly reduce excavation and soil disturbance, preserving valuable land and crops.
Customizable Ground Screw Solutions: As a professional ground screw manufacturer, we provide custom lengths and flange diameters to meet diverse project requirements.


Parameters
Material: | Hot Dip Galvanizing Q235B |
Outer Diameter: | 76mm |
Thickness: | 3-3.5mm |
Length: | 1000-3000mm |
Flang Diameter: | 200mm&220mm |
Application: | Solar Lighting |
Solar ground mount | |
Bollard Lighting | |
Awnings | |
Warranty: | 10 Years |
Service Life: | 25 Years |
Others: | Support Customized |

Ground Screws are the preferred foundations in many solar projects, such as Photovoltaic Solar Farm constructions, Solar Ground Projects, Solar Carports, etc..
Common Types of Ground Screws
Normal Ground Screw, Two Blades, Four Blades, Adjustable Ground Screw
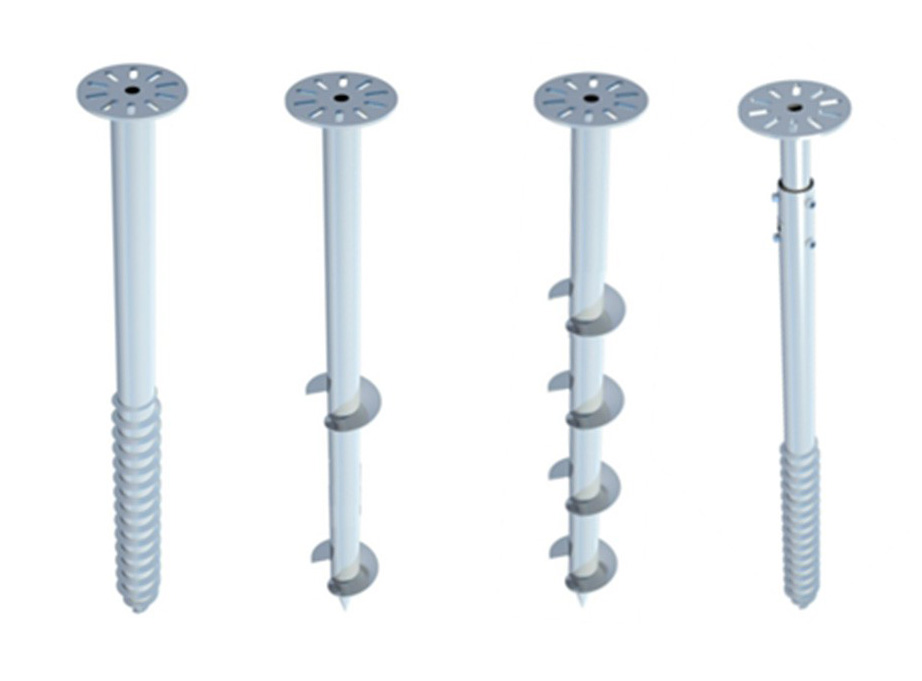
Some other ground screws without flange top as follows for your reference.

Further, customers can place a ground screw order with or without flange top, both are okay.It depends on customers.

Application Examples
Example 1: Solar Farm System


Example 2: Ground Solar System


The Advantages of Ground Screws
1. Environmentally Friendly :
Just pile the ground screw into soil without excavation by using a machine driver.
2. Fast Installation and Save Cost :
By using a machine driver, the ground screw is easily screwed into soil with high efficiency. Ground screw is a better way to save labor cost.
3. Flexible Applications :
The screws could be used in shallow beach, grassland, desert, Gobi and other geological condition environment, and the installation will not be affected by water, frozen soil when installations in harsh climate.
4. Excellent Property :
Using mechanics software, to guarantee it could meet the mechanical requirements in a variety of geology environment and the snow pressure.
5. Durability:
They are made of Steel Q235 with surface finished by Hot Dipped Galvanized and Salt spray test. The ground screws are anti-aging, waterproof and anti-corrosion.
Helical Ground Screw Manufacturing Process
Our helical ground screws are manufactured using high-quality Q235 welded steel pipes. The production process involves several key stages to ensure durability and longevity:
- Cutting and Forming: The Q235 steel pipes are precisely cut and then formed into the desired shape for the helical blade and shaft. Accurate shaping is crucial for the screw’s performance and stability.
- Welding: The formed components are carefully welded together by skilled professionals. Quality welding is paramount to the structural integrity of the ground screw. Issues such as sand holes, incomplete welds (lack of fusion), and inconsistent weld widths are strictly avoided to prevent premature failure.
- Pickling (Acid Washing): The welded ground screw undergoes a pickling process using acid to remove surface impurities and scale. This stage is crucial for proper adhesion of the protective coating. Poor pickling quality will compromise the screw’s corrosion resistance.
- Hot-Dip Galvanizing: The pickled ground screw is immersed in molten zinc to create a robust, corrosion-resistant layer. The duration of the galvanizing process and the thickness of the zinc coating are precisely controlled to meet specific performance requirements, ensuring extended service life. This is a critical step influencing the ground screw’s lifespan.
- Quality Control: Throughout the manufacturing process, stringent quality control checks are performed to verify that each ground screw meets the required standards. This includes visual inspections for weld quality, coating thickness measurements, and dimensional accuracy assessments.

Key Considerations:
- Materials: Q235 welded steel pipes are the main raw material, chosen for their structural strength.
- Corrosion Protection: The pickling and hot-dip galvanizing processes are essential for providing superior corrosion resistance and extending the lifespan of the ground screw.
- Lifespan: Under normal conditions, our helical ground screws are designed to last for 20 to 30 years.
- Environmental Factors: Factors such as soil acidity and proper installation techniques affect the lifespan of the ground screw. Improper handling or usage can damage the protective coating, accelerating corrosion and reducing its service life.
Testing the Load-Bearing Capacity of Helical Ground Piles
Ensuring the load-bearing capacity of helical ground piles is crucial for the safety and stability of any structure they support. Various testing methods are employed to verify that these foundations can withstand the anticipated loads. Here’s an overview of common testing procedures:
1. Static Load Testing (Axial Compression/Tension Tests):
- Procedure: Static load tests are considered the most reliable method. A hydraulic jack or similar equipment applies a controlled, incremental load to the top of the installed helical pile, either in compression (pushing down) or tension (pulling up).
- Measurements: During the test, the displacement (settlement or uplift) of the pile is carefully measured using precision instruments. The applied load is also continuously monitored.
- Data Analysis: The load and displacement data are used to generate a load-displacement curve, which reveals the pile’s ultimate capacity and its performance under various loading conditions.
- Evaluation: This data allows engineers to determine the pile’s safe working load, factoring in an appropriate safety factor.
2. Dynamic Load Testing (Pile Driving Analyzer – PDA):
- Procedure: This method utilizes a Pile Driving Analyzer (PDA) system to measure the pile’s response to impact forces. A hammer or drop weight applies a known dynamic load to the top of the pile.
- Measurements: Sensors attached to the pile measure the force and acceleration, allowing calculation of pile capacity during driving (or re-driving).
- Data Analysis: The data generated by the PDA can be used to estimate the static capacity of the pile, and it also provides insights into the dynamic behavior of the soil-pile system.
- Efficiency: Dynamic testing is often faster and less expensive than static tests, but it may not be as precise.
3. Pull-Out Testing (Tension Testing):
- Procedure: Pull-out testing specifically assesses the pile’s resistance to uplift forces. A hydraulic jack or similar equipment applies a controlled tensile load to the installed pile.
- Measurements: The applied load and the resulting uplift displacement are accurately measured.
- Data Analysis: This data determines the pile’s capacity to resist tension loads, which is vital for applications exposed to wind or uplift pressures.
- Relevance: Especially useful for structures that experience significant uplift forces such as in high wind environments or foundations for signs and solar arrays
4. Lateral Load Testing:
- Procedure: Lateral load tests are used to evaluate the pile’s resistance to side forces. A controlled lateral force is applied to the pile’s top.
- Measurements: The applied load and the resulting displacement (deflection) are meticulously measured.
- Data Analysis: This testing gives critical data for installations that may be subject to horizontal stresses, such as for structures that encounter wind or seismic activity
- Relevance: Especially useful for structures that experience horizontal forces such as fences or retaining walls.
Key Considerations in Testing:
- Soil Conditions: The test results are highly dependent on soil conditions at the testing site.
- Pile Specifications: The testing method must align with the specific pile type and the application requirements.
- Professional Oversight: Load testing should be performed by experienced professionals who are knowledgeable about the testing procedures and data interpretation.
- Safety Precautions: Strict safety measures are essential during all testing operations.
Importance of Load Testing:
Load testing is an essential part of ensuring the reliable performance of helical ground piles. These tests provide invaluable data for confirming structural integrity, optimizing design, and minimizing risk. Properly conducted tests guarantee the longevity and stability of any structure supported by these foundations.

Helical Ground Pile Operation Conditions
The following conditions must be met before commencing helical ground pile installation:
- Project Documentation:
- Geological data, construction drawings, and the construction organization design are complete and available.
- Site Preparation and Clearance:
- All surface and subsurface obstacles within the construction area have been removed or addressed. The site is leveled, and soft areas that could affect the operation of construction equipment have been appropriately treated. Drainage measures are in place.
- Utilities and Infrastructure:
- Water, electricity, access roads, and temporary facilities for construction are ready for use.
- Survey Control:
- Survey reference lines and elevation benchmarks have been established on-site and are properly protected.
- Trial Piling in Complex Soil:
- In complex soil layers, trial piling should be conducted prior to full-scale installation, with a minimum of two test piles installed.

Hot-Dip Galvanized Solar Ground Screws: The Ultimate Foundation Solution
Looking for a robust and reliable foundation for your solar projects? Hot-dip galvanized solar ground screws provide a superior alternative to traditional concrete footings. These innovative foundations offer unmatched durability, speed, and versatility, making them ideal for a wide range of applications.
What are Hot-Dip Galvanized Solar Ground Screws?
Material & Corrosion Protection: Typically crafted from high-strength Q235 carbon steel, these ground screws feature a hot-dip galvanized coating for exceptional corrosion resistance, ensuring a long service life even in harsh environments.
Versatile Specifications: Our solar ground screws are available in a wide range of sizes, with lengths spanning from 100mm to 3000mm, outer diameters ranging from 76mm to 102mm, and thicknesses from 3.0mm to 3.5mm.
Exceptional Performance: Designed for superior load-bearing capacity, these ground screws are renowned for their solidity, anti-settlement, and anti-pullout properties, making them suitable for diverse geological conditions including clay, Gobi Desert, gravel, and more.
Wide-Ranging Applications: Solar ground screws are not limited to solar projects! They are widely used for photovoltaic power station pile foundations, billboard foundations, sign and flag foundations, wooden house foundations, and more.
Simple and Effective Construction: The design includes a strong steel pipe core, a top connecting pipe, a drill pipe tip, a middle steel rod, and a bottom connecting shaft. These are directly driven into the ground and used as a secure foundation.
Firstsolar is an international PV mounting systems manufacturer that integrates R&D, design, production, marketing, sales, and professional after-sale service. XIAMEN FIRST TRADE CO., LTD has 3 plants covering an area of 20,000 square meters. We are sincerely looking forward to cooperating with you for a mutually beneficial, win-win partnership.
Help Center
Have a query? Please check this question and answers
Firstsolar has own factory with more than 80 skilled and experienced workers,the productionline is strictly in accordance with high standards and attach great importance to quality controland inspection.
Of course, our first-class production engineers, technicians and R & D team offer innovativedesign and reliable solution to customers based on more than 8 years of experiences.
Yes,Firstsolar has provided OEM service,design service and buyer label service for more than10 years.
Yes the products of Firstsolar have been certified by lSo, sGS,TUVand AS/NZS 1170.2.
It depends on actual order quantity and your special requirements. Generally, it will be 1-2weeks.
lf total amount is less than US$5000, we need 100% in advance; if total amount is more thanUS$5000, we need30%T/Tin advance